- Company
Specialist Firms Helping Deliver UK’s Fibre Optic Network

The ongoing programme to update the UK’s telecoms infrastructure has meant repurposing large amounts of the existing telecoms network. This requires that old cable ducts are thoroughly de-silted and cleaned in preparation for new fibre-optic cabling. For two specialist contractors in the UK, the use of equipment reconfigured specifically for the task is proving indispensable.
To meet the demand for ultra-fast broadband, £12bn is being invested in the UK’s fibre-optic infrastructure to provide 1Gbps capable Fibre-to-the-Premises (FTTP) broadband to over 20 million premises by the mid to late 2020s.

Milton Keynes and Northampton based D&A Commercial Cleaning, a Tier 1 operator, is one of a handful of UK contractors specialising in the de-silting and high-pressure jetting of telecom cable ducts and comms boxes.
Managing Director Dave Angel says that his team originally used gully machines removing the build-up of deposits in the ducts and boxes, but there were several issues with this method.
“Firstly, we needed something with more power,” he says. “The accumulated silt in the ducts is like concrete and it was taking a long time to remove.”
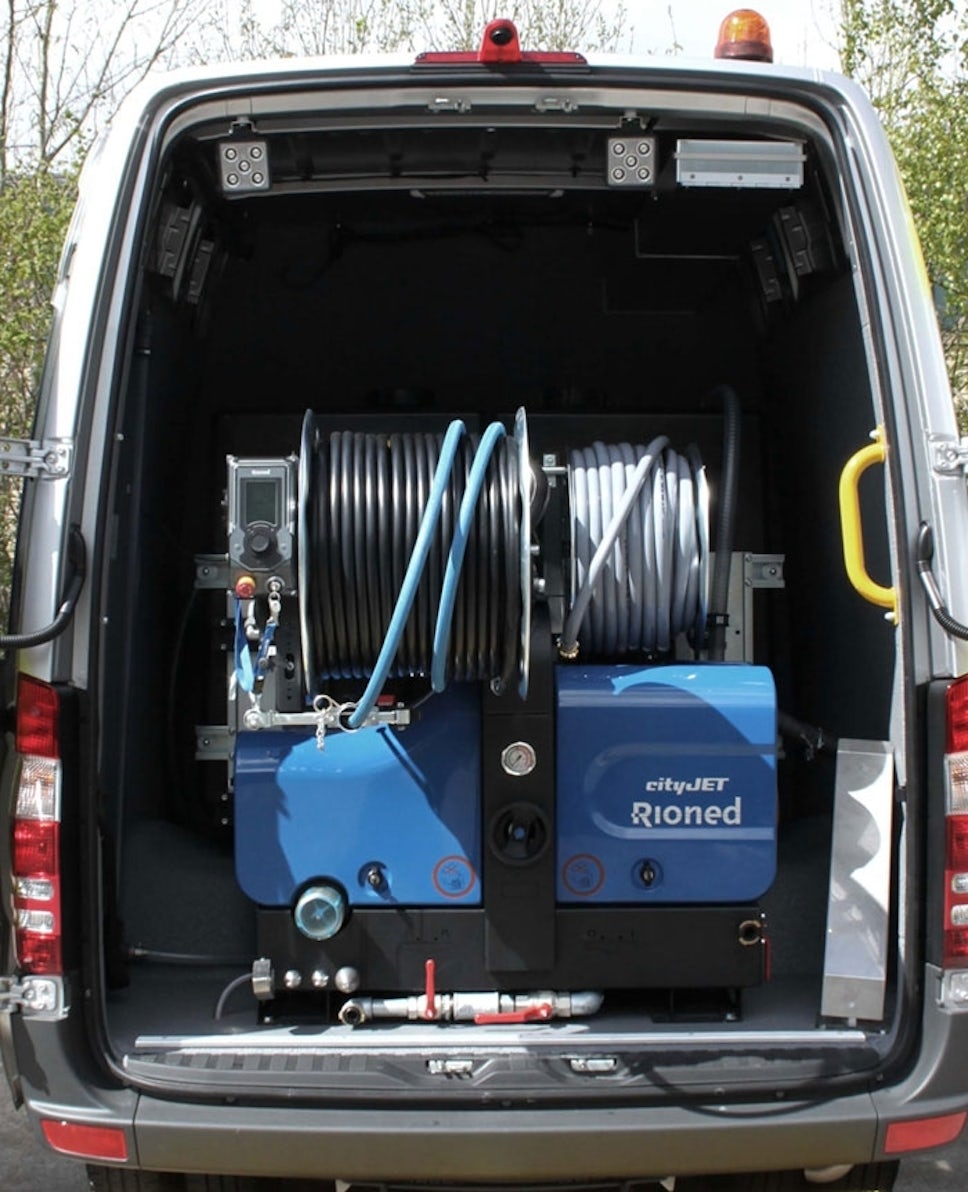
Already familiar with Rioned equipment, D&A approached the firm about finding a solution. The CItyJet seemed like an ideal solution; a low-weight, high-performance van-pack jetting unit producing pressure up to 3600 psi/13 gpm that was more than capable of removing solidified deposits.
To meet the specific requirements of the D&A team, modifications were made to the standard CityJet unit, including the installation of the RioPulse pulsator system for improved hose feeding and retrieval.
The pulsator unit operates by creating a vibrating or pulsing action on the hose when using pressurised water. The pulsing action minimises hose drag by reducing the surface contact of the hose, propelling it further and faster into the duct. The pulsator also reduces water use by a third, meaning the teams can jet longer on site.
Further modifications comprised installing 250m of 1/2” hose for better access and travel distance in the 50mm cable ducts.
The results are 100% better,” explains Dave. “We’re doing the work a lot quicker than before with the help of the Rioned system. We’ve also just bought another more powerful jetter for de-silting that will be fitted in a new van next week.”
MDL Plant Ltd, based in Bury St Edmunds, undertake the same kind of work but primarily use RioCom jetvac combination units.
MDL Plant Director Paul Snow says they wouldn’t have anything else: “As tanker units handle more water, it means that rather than having to hire in tankers, we can use the powerful suction pump of the RioCom to clear out heavily silted manholes before the jetting. The combination unit can do both jobs, making it more economical for the client.”
“On one occasion we cleared silt from a 350m line in a single run. We obviously had to keep adding hose to accomplish it, but the unit will handle 250m runs all day.”
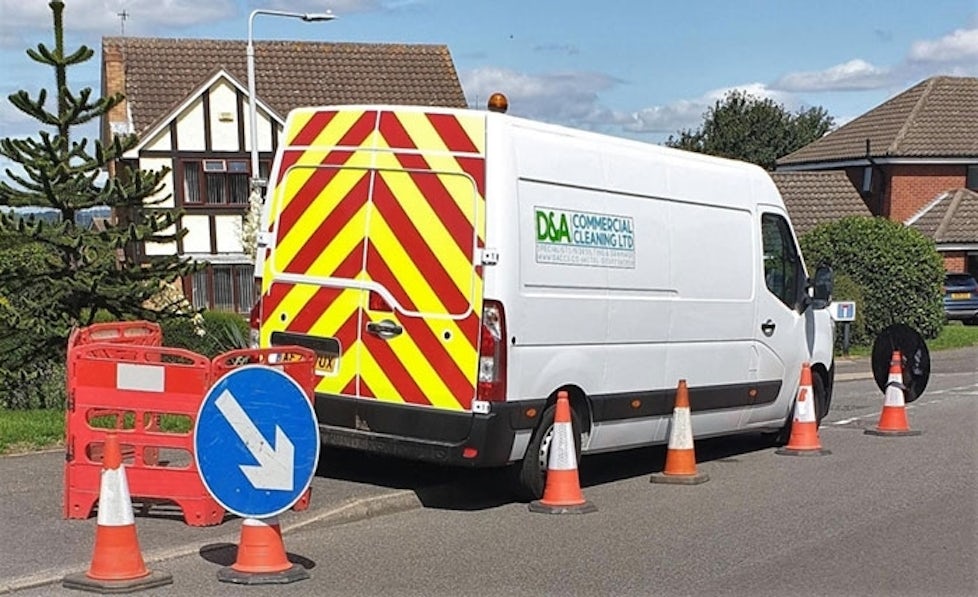
The RioCom jetvac combination unit has been specially adapted to suit the desilting task, with a jetting capacity of 4000psi @ 12 gpm and a pulsator unit. Paul explains that duct cleaning is a balancing act that requires the jetting power to remove the hardened silt without causing damage to the existing telecoms cabling.
“We now have three combination units with another one due to be delivered shortly. It’s quite a new process and Rioned has worked closely with us to get the equipment right as we’ve grown.”“The new fibre optic cabling is installed alongside the old copper infrastructure so we can’t use too much pressure without damaging the existing cabling. The RioCom is a fantastic bit of kit and we have about a 75% successful clear rate using the equipment, which is really good when taking into account the age and wear and tear on the ducts.”
Rioned’s UK Sales Manager Mark Cox says Paul and his team were instrumental in the rise in popularity of small combination units being used for this type of work: “We invited Paul over to the factory in the Netherlands to show him a base unit and from there we designed the exact specifications that he needed for optimal desilting works.”
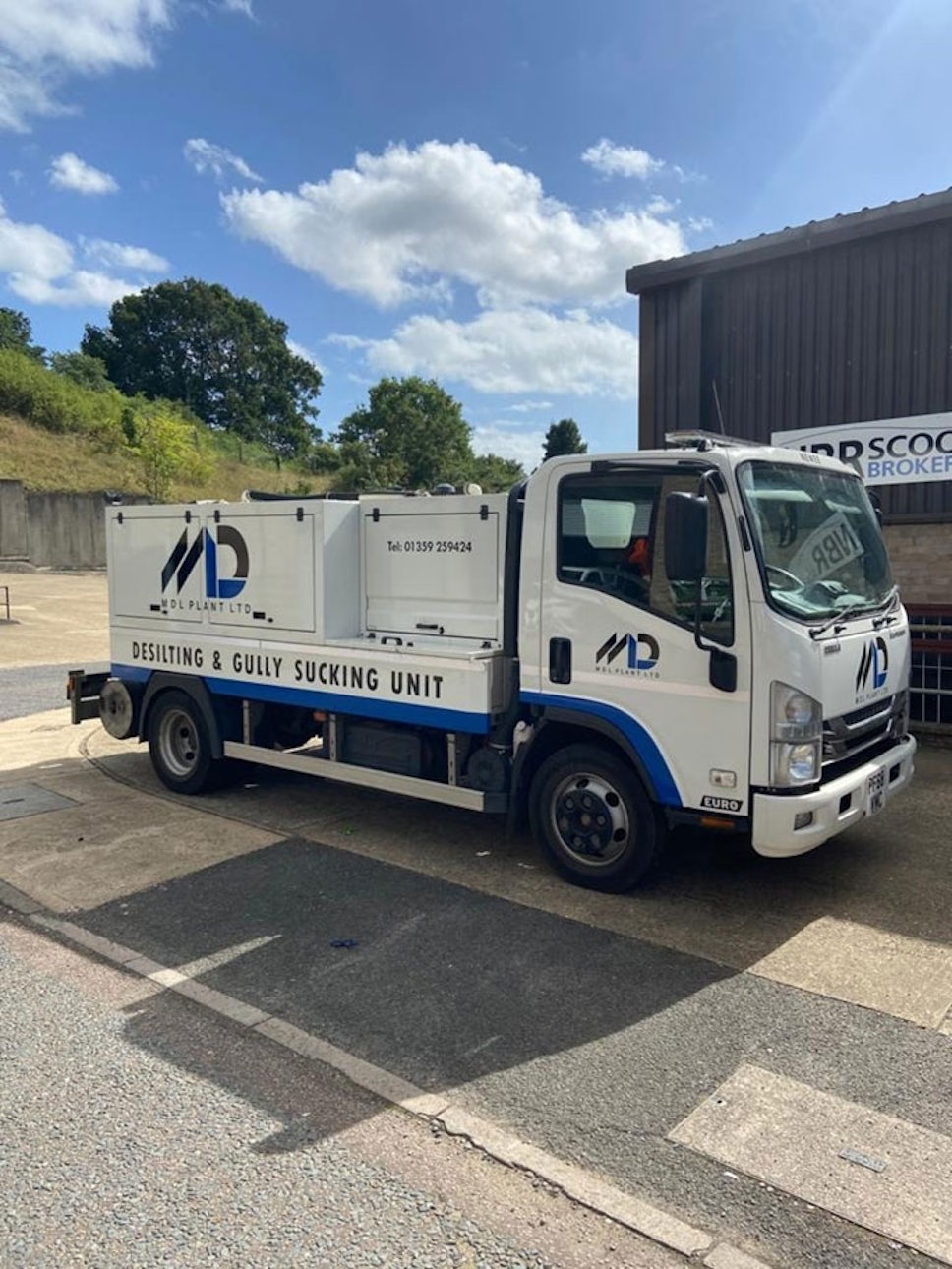
“Due to the firm’s geographical area of work, Paul needed maximum water capacity and optimum performance so we designed a unit that can work on-site for over 75 minutes continuously without needing additional water, which is more than enough for even the toughest of desilting works.”
“We are always pushing the boundaries of what we can achieve by working with specialists such as Dave and Paul to make sure we deliver equipment that exceeds expectations for them and their clients.”
- Company