- Guides
5 Essential Safe Practices for Drainage Contractors
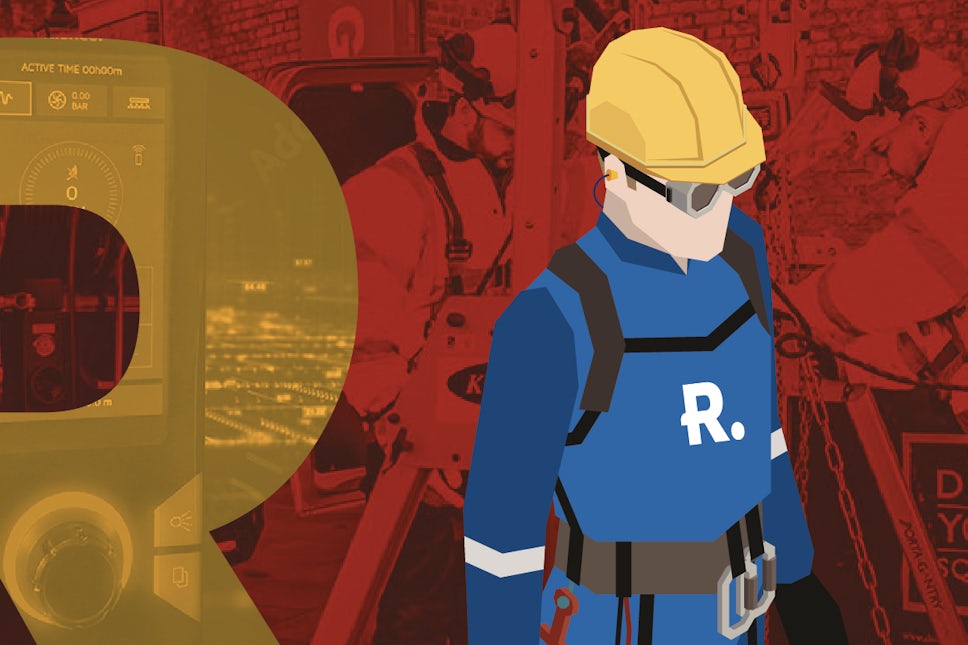
There are many hazards associated with working in the drainage sector, with the misuse of high-pressure equipment having the potential to cause severe injury or even death. To mitigate against accidents, most contractors ensure that employees undertake nationally accredited jetter and safety courses regularly. This blog details our top five tips to ensure the safe operation of a range of drain jetting equipment.
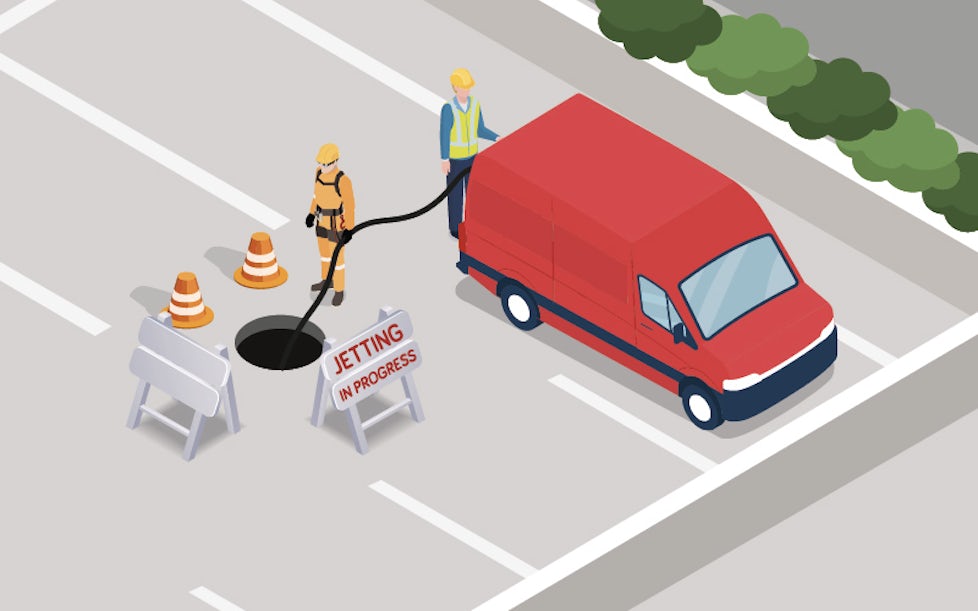
1. CONDUCT A RISK ASSESSMENT
High-pressure drain jetting equipment should never be operated close to customers, the public or animals. To reduce the risk of unauthorised access to the work area, contractors should position warning signs and beacons, and create a cordon around the jetting site using protective barriers. When working in public areas, this should also include using hose covers to protect the public against tripping or injury due to hose failure.
Before commencing jetting activities, operatives should carry out a full risk assessment of the jetting site, including checking for any loose items to avoid projectiles, and ensuring that the surface underfoot is safe and not slippery.
These checks also include evaluating the effects of the noise pollution created by high-pressure jetting activities and any actions that can be taken to reduce it. This has been a careful consideration in the development of Rioned equipment, with portable, trailer, and van-pack jetters designed with protective cases to reduce engine noise, while the all-electric eCityJet machine, powered by six Li-ion batteries, offers virtually noiseless operation.
When working at night or in bad light, operators should utilise a range of lighting to ensure that the work area is well lit before commencing any jetting operations. A wide range of lighting solutions, including warning lights, beacons, work area and interior lights can be installed in van-pack jetters and jetvac combination units.
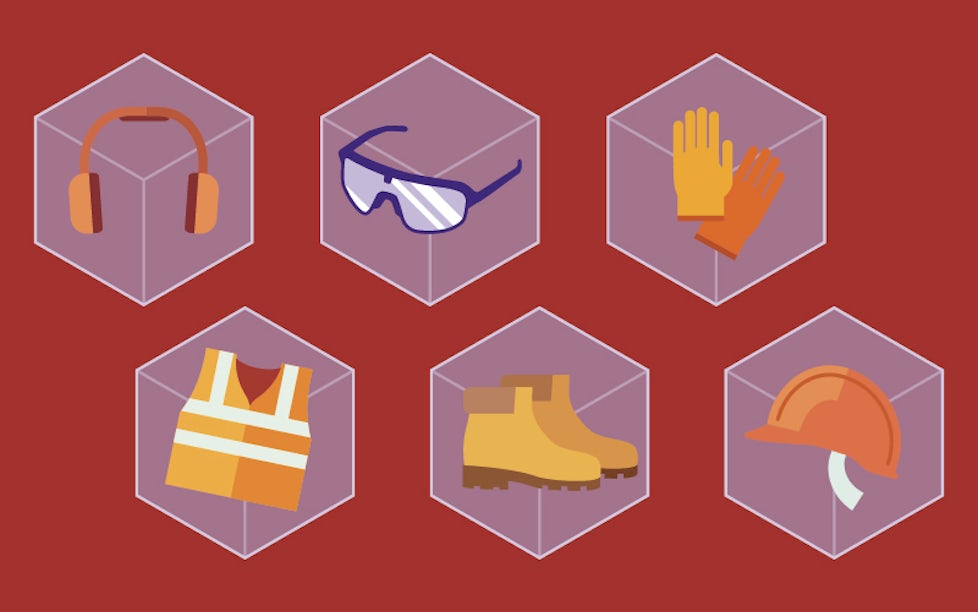
2. WEAR THE CORRECT PPE
Water jets as low as 100 psi can penetrate and cut through skin, so it is essential to always wear the correct PPE (personal protective equipment).
Splashback from jetting operations may contain contaminants and hard debris travelling at speed, therefore wearing the correct PPE can greatly minimise the risk of serious injury and disease. When working with water pressures above 2000 psi, operators should wear a full face shield as a jet travelling at this speed is capable of removing an eyeball from its socket.
Before beginning any drain jetting tasks, you should ensure that you are wearing a range of protective clothing including:
- Ear Protection (LWA 109dB)
- Eye Protection – Helmet with Chin Guard or Visor, Goggles, and Face Shields
- Hand Protection – Rubber or Waterproof Heavy Duty Gloves
- Waterproof, High-Visibility Clothing
- Rubber Spray Boots with Metatarsal (Foot) and Toe Guards
- Head Protection – Hard Hats

3. ENSURE EQUIPMENT IS OPERATED CORRECTLY
Personnel that operate high-pressure equipment should be suitably qualified and authorised to use the machine. It is most often the responsibility of the contractor to ensure that operators are issued with the correct documentation before commencing any jetting works.
Based on near misses and engineer experiences, below is are tips for the safe operation of equipment:
- Never operate a jetter that has not been regularly serviced in line with the manufacturer’s guidelines.
- Never operate high-pressure equipment if you are under the influence of alcohol or other substances.
- Always check the high-pressure jetting hose and attachments to ensure that they are free from kinks, blockages and damage before turning on the jetting machine.
- The high-pressure pump should not be engaged until the jetting nozzle is at least three feet from the entrance to the drain or sewer.
- Use either a metal guidance ring or leader hose attachment to provide a visual warning when the jetting nozzle is close to the pipeline opening.
- Control the high-pressure hose or hose attachment with both hands.
- Do not block the control levers or hydraulic parts when in use – this includes leaning on machinery or resting additional equipment on the machine.
- Fully ventilate the drainage van while the jetting machine is in use to prevent fires and carbon monoxide poisoning.
- Always turn off the supply to the high-pressure jetting nozzle before it is removed from the pipe opening.
- Always depressurise the high-pressure circuit unit before commencing jetting work and when you have finished using it.
- Set the pressure of the spray gun to half the maximum pressure before the machine is started and never exceed the maximum pressure marked on the manometer.
- Never place your fingers in front of the jetting nozzle or into the venturi pump inlet.
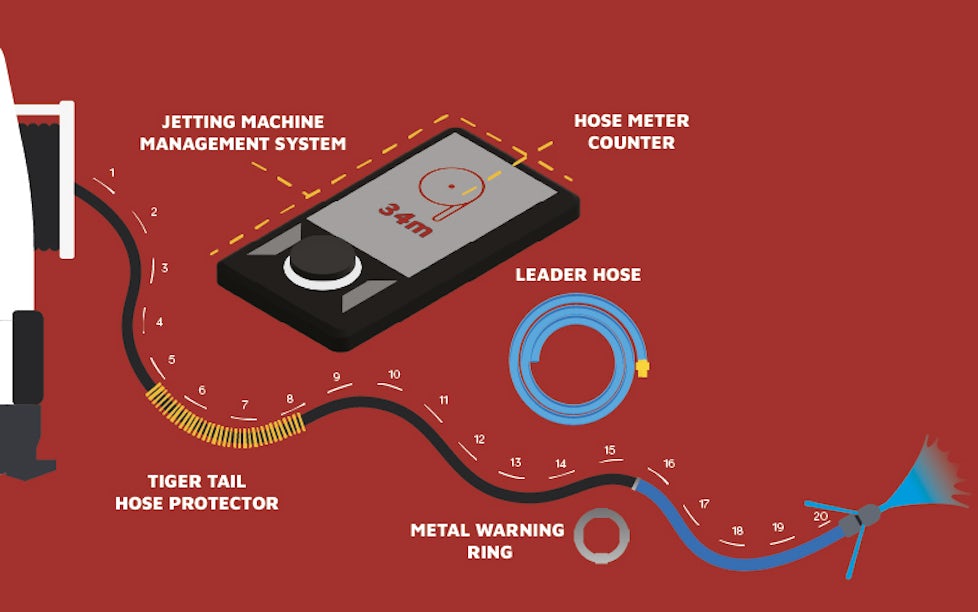
4. USE SAFETY EQUIPMENT ACCESSORIES
Safety technology in the drainage industry has developed rapidly to enable safer working practices. Below are a few examples of equipment designed with safety as a priority:
- Jetting Machine Management System – Machine Management systems, such as the eControl Touch, provide essential system warnings that help avoid critical failures in machinery and parts, and accurate real-time readings of water usage, pressures and flows. When used in conjunction with Radio Remote Controls, machine management systems can also send warning messages to operatives even when controlling the machine at a distance.
- Leader Hose or Hose Warning Ring – A leader hose is a short (3m or 5m) length of brightly coloured hose that connects directly to the end of the main jetting hose as a warning to the jetting operative that the jetting nozzle is close to the entry of the sewer or drain. Similarly, some manufacturers include a metal ring positioned at 5m from the hose end to provide a visual warning of when the nozzle is nearing the manhole.
- Hose Meter Counter – A Hose Meter Counter measures the amount of hose that has travelled down the drain and can be used as an indicator of when the jetting nozzle is close to the drain or sewer opening.
- Whip Checks – Whip Checks are an important safety device used to prevent high-pressure hoses from whipping back towards the jetting operative if the hose becomes separated from its fitting. Attached to the join of two hoses or fixed to a pump or hose attachment, this device restricts the movement of the pressurised jetting hose.
- Tiger Tail Protector – ‘Tiger Tail’ sleeves, such as the RioProtect, are a cost-effective way of extending the life of high-pressure hoses that are subject to wear on contact with drain and sewer openings.
- Roller-Upper – Used to carefully lower or retrieve hoses and cable from pipelines, this easily adjustable accessory is placed over the entrance to the drain or sewer and is particularly useful in restricted access areas and situations where the hose reel cannot be placed close to the pipe entrance.
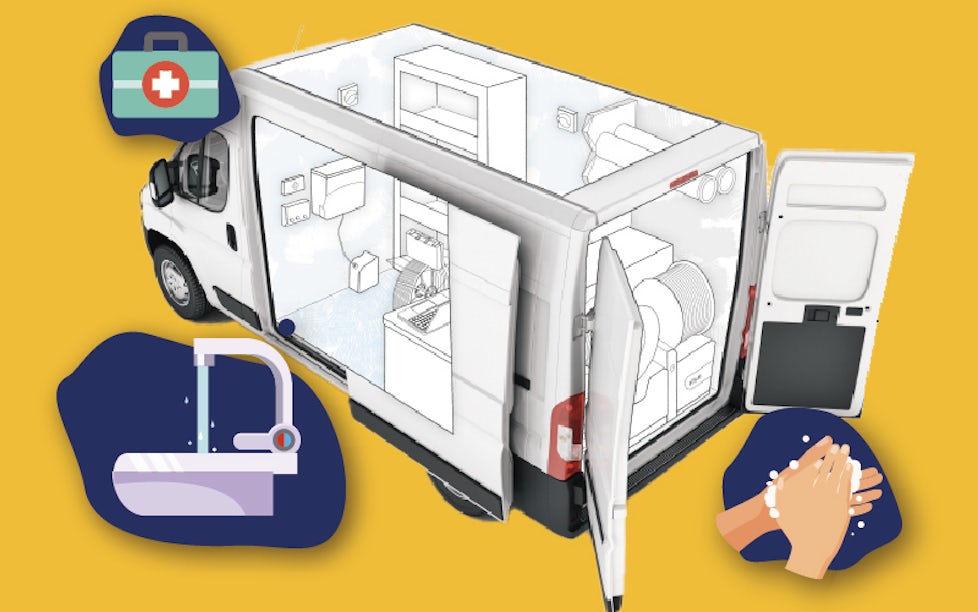
5. INSTALL A WELFARE STATION
Protecting workers and customers against bacterial contamination and the biological hazards of drain cleaning is extremely important. Drains harbour dangerous bacteria and other infectious micro-organisms and materials that can cause serious illnesses or death.
To minimise the risk of contamination, operators should always wear the correct PPE and avoid exposing their eyes, hands, nose, mouth and ears to any wastewater, including any cuts or abrasions. Jetter water tanks should also undergo thorough cleaning at least every six months with water above 70 degrees (160 Fahrenheit) to prevent bacteria that may cause Legionnaire’s Disease.
On-board welfare stations are an increasingly common addition to modern multipurpose vehicles to further protect operatives from the dangers of drain and sewer jetting. If necessary, operatives should flush their mouth, eyes and nose with clean water, wash their hands and arms, and clean any clothing and surfaces that have come into contact with any potentially infectious materials. On-board welfare stations most commonly comprise the following:
- Hand wash units
- Eyewash stations
- First aid kits
- Fire extinguishers and blankets
- Guides